Press-setting
frequently asked questions
|
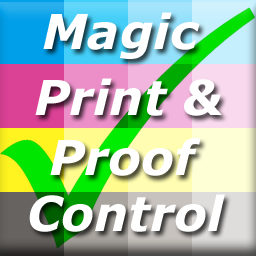
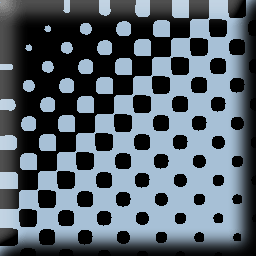
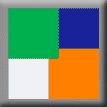
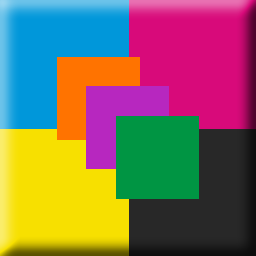
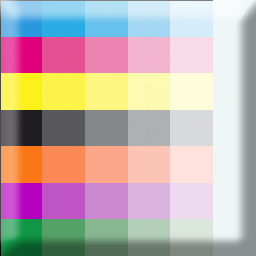
|
All press-setting applications:
Which spectrophotometer model
should I use?
You
can use many 45/0° models with Colorsource press-setting applications,
thanks to using standard CGATS spectral measurement files you can
easily produce with a wide range of instruments and applications.
Originally,
we designed our applications for use with X-Rite i1Pro family (or the equivalent
EFI ES-x O.E.M. models), for taking advantage of their fast-scanning mode and
their excellent price/performance ratio. Today, the affordable 45/0°
spectrophotometers such as i1Pro, i1Pro 2, i1Pro 3 or MYIRO-1 replace
quite advantageously the best and most expensive proprietary pressroom
spectrophotometers such as eXact, eXact 2 or FD7:
Much more productive AND much cheaper.
Colorsource
applications for pressroom can process the spectral (and
non-spectral) measurement files of one to ten colors charts, measured with classic spectral
ranges such as 380-730, or 400-700 nm or else.
With Colorsource, you can use your spectrophotometers in M0
or M1 measurement conditions: i.e., with the spectrophotometer internal light
source matching C.I.E. A illuminant or C.I.E. D50, with no UV-cut filter. The applications may work when
using a UV filter but mind ISO12647-x and G7/IDEAlliance standards
target colors have been measured with no UV filter, so that small
differences may occur.
With or without UV filter, differences in paper
tints may still occur when using uncoated papers because of ISO12647-x
paper tints specifications. For more details on these issues, please refer to our regularly
updated paper about
color printing
and proofing standards and to the
applications user's
guides.
We
think it is not worth using any more expensive spectrophotometer model,
for 95% of publishing and packaging commercial print applications. Hand-held 45/0° proprietary pressroom spectrophotometers with
useless built-in functions are obsolete equipment, because they are
very expensive without bringing any significant advantage in real life
in terms of accuracy. And using them efficiently in the Print House
would anyhow require
connecting them to a PC running dedicated software!
Moreover,
for optimal safety at lowest cost, we advise you owning and using TWO spectrophotometers:
For
example, when producing color proofs, you should use one spectrophotometer for
calibrating and characterizing your color proofing system, and a second
spectrophotometer for checking your proofs control bars. Because if using
only one spectrophotometer and it becomes faulty, you will make mistakes when
characterizing your color proofing system, and then
the same mistakes
when controlling your proofs. So that you will happily certify bad
proofs!
By the way, this is showing - once more - that
all the so-called
"ISO 12647 Color certifications" as they stand, are a pure joke: it
will always belong to
professional Proofs Users and Print Buyers doing their job by
controlling all color proofs and prints by themselves. |
All press-setting applications: Where should I buy my
spectrophotometer?
We still see nowadays some Vendors explaining our French
customers that
Eye-One Pro CANNOT measure lithographic offset plates, because it is a spectrophotometer!
In addition, they often explain their Prospects, depending on their budget, that Eye-One Pro is NOT accurate enough
for doing a professional print job and they should spend MUCH more money!
Actually,
our 40 years' experience on many different professional digital imaging
markets, including 29 years shared on the Graphic Arts market, shows us that
Graphic Industries is the market
where the more lies are told to customers, and where ALAS the larger
numbers of customers are still found trusting lies!
We
still see far too many lies told to Print Buyers as well. Because when smart qualified Graphic Industries Professionals duly
refuse buying bad or uselessly expensive equipment, some Vendors try - and often
succeed!
- convincing some incompetent Print Buyers that they should impose
these bad tools to their Supply Chain!
This is how
so many bad and
uselessly expensive color-proofing systems, and so many other products,
have been successfully marketed, even when cleaver and qualified Print
Producers duly
refused them. Of course, ALL Print Buyers and Printer Producers are paying for the
bill of this persistent marketing bullshit that is quite specific to
Graphic Industries.
Some
people believe that anyhow, wasting a few dozen thousand dollars by
making some non-optimized investments on small equipment has no
importance, when compared with the million dollars investments required
for big printing machinery. However, we believe this may be the tree hiding the forest:
because there are no reason why heavy-investment tools would be optimized
and properly used, when some Vendors can still rely for
marketing their products on customers technical
approximations and deep misunderstanding of modern print technologies.
We
consider persistent lies from some Vendors to Graphic Industries,
and so much bad information, are killing Graphic Industries. Therefore, Graphic Industries Professionals should train
properly in order to protect themselves from lies that cost them a lot
of money. They are the color quality Experts or they should be.
Professional Print Buyers should train
properly as well, in order to optimize their Supply Chain, install the appropriate
color quality processes, and advise properly they Supply Chain, rather
than putting them in trouble with bad advises and uselessly expensive
investments.
Most of Graphic Industries professional organizations are not
doing their job for protecting their own interests. Otherwise,
marketing bullshit would have stopped many years ago.
So
that as a conclusion, we can only strongly advise you training properly with
experienced Professionals completely independent from market Vendors,
and buying your instruments at lowest possible price on Internet. (Of
course, if prices look too good, do not pay cash in advance ;-)) |
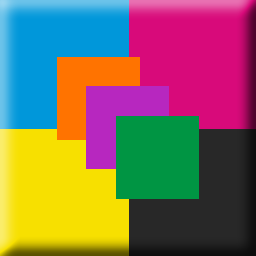
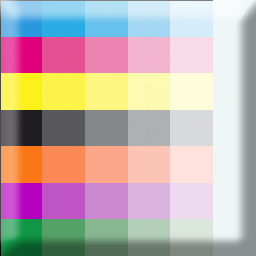
|
Press-setting
applications: Should I afford a pressroom scanning spectrophotometer for setting my
offset press ink keys color bars?
Pressroom
scanning spectrophotometers are good tools for getting more
productivity at press-setting stage, but we find in the field most of
installed systems are hardly used, because they are badly installed and
parameterized, and Staff is not trained properly. Apparently, many Print
Houses find they are a kind of decorative element on their presses.
Colorsource
press-setting applications are an excellent tool for programming properly all Market pressrooms scanning systems. Moreover, our
experience proves that if a Print House is not able to set
perfectly all their printing presses by using Colorsource applications, there is no chance they will
manage it with their expensive scanning systems, which sometimes do not
even guide them for setting the optimal solid inks densities! So that an excellent
and quite affordable learning curve for any Print House consists into mastering
their presses with
Colorsource press-setting applications first.
Moreover, Colorsource
press-setting applications allow you specifying, recording and communicating
all your one to ten colors print standards, and managing all the associated
print form correction curves for each ink on each press. |
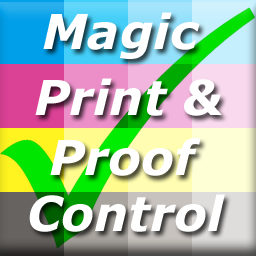
|
Free Magic_Proof_&_Print_Control: What control
bar should I use?
Our free Magic_Proof_&_Print_Control software allows you to check all the
classic CMYK control bars that you will find on the proofs, such as the UGRA/FOGRA
Media Wedge 2 & 3, G7/IDEAlliance 2009 or 2013 and Colorsource
ISO12647-7 bars.
G7/IDEAlliance bars are royalty-free. You can therefore freely incorporate them
into the proofs you produce. You can find details about this American standard
in our ISO12647 standards document on
the
ISO12647-2-3-4-6-7 standards page.
Please note that the UGRA/FOGRA Media Wedge 2 & 3 control bars are not
royalty-free, so you should pay a license if you want to incorporate these
control bars into your own color proofs.
Colorsource ISO12647-7 control bar is a royalty-free control bar optimized for
proof and print control. So, you can freely incorporate it into your proofs. You
and your Partners will then be able to control these events free of charge with
Magic_Proof_&_Print_Control.
Magic_Proof_&_Print_Control software
also allows you to use your own control bars and specify your own aim colors, by
using a reference measurement file (Fingerprint), or using a specified and saved
print standard using the MagicPrepress software. In this case you can
control all digital and traditional printing configurations using one to ten
inks, and not only CMYK prints and proofs. |
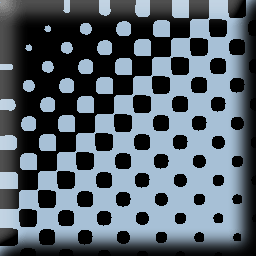
|
PLATE
application: What is the difference with using a dedicated Plate Reader?
Historically,
the offset plates were controlled by using a specific "Plate measurement
option" on CMYK densitometers. This always produced good results,
although densitometer's plate measurement option did not take into
account the plate model for optimizing its optical filtering wavelength.
Using
a spectrophotometer with PLATE application is a quite a better (and
cheaper!) solution, because PLATE application analyses the
color of your plate model and optimizes its optical filtering process, in
order to produce even more accurate results than optical densitometers.
Moreover, PLATE application allows you averaging your measures on
various plates with different screen angles, for even better accuracy.
Nevertheless,
it is true that (good) plate readers may bring you some advantages, for following
reasons:
1)
Plate readers working process is quite different: The instrument makes
plate digital microphotography's, and then uses image analysis in order to directly assess your plate dot geometrical areas, so
that you do not need calibrating first the N-Factor of your plate
model.
While
computing accurate geometrical dot areas from the optical
densities' measurements produced with densitometers or spectrophotometers, first
requires measuring the N-Factor of the plate model you are using: We believe this operation is fast and easy
with PLATE application. For more details about
N-Factor and how to measure it with PLATE application, you can
download and read the application user's guide.
2)
Your plate model N-Factor can slightly vary depending on the location
where you measure it on a plate. So that you may find 0 to 0.5 %
differences between a (good) plate reader and PLATE application
results.
Of
course, these potential very small differences between the results of a
plate reader and PLATE application will have no consequence at
all on the final print quality, because in the end MagicPrepress
application will produce perfect prints meeting
the TVI curves you expect.
As
a conclusion, we have often advised big Print Houses owning all the
other necessary control tools to invest into a good plate reader, but we
consider this investment is NOT a priority for any Print House that does
not own all priority equipment such as Eye-One Pro
spectrophotometer.
If you are a Company where buying a
plate reader can reasonably be envisaged, we advise you investing into a plate
reader able to measure your geometrical dot areas, not only on your offset
lithographic plates, but also on your color prints. Because coupled with using
your spectrophotometer, this will allow you measuring both the optical
and mechanical parts of your press dot gains: No use at all for your day-to-day work, but quite useful as a press diagnostic tool, if your print
process shows abnormally high dot gain curves.
Because MagicPrepress application
allow you compensating very high dot gains with very good accuracy, but
abnormally high mechanical dot gains mean that your press is in bad
conditions and you should consider solving this problem for optimal results and
print stability.
According
to our own experience and our expert customers, offset plate readers models
such as X-Rite iCPlate or Techkon SpectroPlate are quite
good instruments. If you buy iCPlate, we advise you buying the
version including geometrical dot area measurement on prints.
Of
course, they may be other good models on the market that we do not know,
but in all case, we think buying more expensive models than iCPlate
or SpectroPlate is a pure waste of money. For example, you should rather not
buy a 4000+US$ plate reader model that makes 4 to 5% measurement errors
when unplugged from mains and working on its internal battery ;-) |
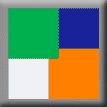
|
Inks Color
Quality control: How should I specify and communicate a spot color?
Any
properly designed swatch book should specify each spot color not by a
mere Lab D50 2° (or else) apparent color, but as full visible
reflectance spectrum: This is the only way for fully specifying the
color, as you will perceive in any lighting and viewing conditions.
The
colors you perceive on a physical swatch book, in your appropriate
viewing conditions, are always printed with errors. Because it is
impossible to formulate perfectly hundreds of different inks, and then
print each of them with perfect appropriate ink thickness.
The
real swatch book errors will be acceptable or not, depending on each
tint and on your tolerances. However, no tint on a swatch book should be
considered reliable, unless you have measured this tint on your swatch
book and compared it
with its specifications in your digital spectral inks' library.
All
Print Buyers and Print Producers on any Supply Chain must refer to the same spectral data
for spot colors communication and reproduction, without dumb and inappropriate marketing changes of
these swatch books specifications that oblige all market Actors to
update all their software applications, and create many ambiguities and
mistakes. GretagMacbeth
initiative for promoting the royalty-free spectral library CxF file format
(Color eXchange Format acronym), where all PANTONE tints official
reflectance spectra were published for a low-cost license (~ 53 US$) and
accessible with using free "CxF reader" i1Share
application was an excellent initiative. However, apparently these market
transparency efforts have been dropped
since X-Rite acquired GretagMacbeth... and PANTONE. Any
marketed swatch book claimed as being standard should have its full
technical specifications published and accessible to all involved
Professionals on the Supply Chain. Print
Buyers and Print Producers should refuse using any swatch book that is
not clearly specified by a spectral data library, and we think Print
Industries professional organization should have asked a long time ago these standard spectral
data libraries be published as ISO standards with their full
specifications! |

|
How
can you get the PANTONE up-to-date spectral data for controlling them
before you install them on a press, and for controlling all printed PANTONE inks?
For
controlling your PANTONE inks prior to installing them on your printing
press, and for controlling your printed PANTONE inks, including the ones printed
on your PANTONE swatch books, you need knowing the official up-to-date spectral
reflectance' data that are published by PANTONE.
MagicPress, MagicPrepress
and free Magic_Proof_&_Print_Control can use native
CGATS and CxFv3 formats for importing their spot colors and special process inks
libraries. And they can re-export CxFv3 as CGATS text files as well.
You
can download and use our free
All_you_should_know_about_PANTONE_and_else_spot_colors.pdf document that allows you making a much better use of all
PANTONE CxFv3 digital libraries.
CGATS
format advantage is that it allows you using your modern PANTONE digital
swatch books with the best applications, including MeasureTool, i1Share,
ProfileMaker ColorPicker module and Colorsource SPOT_Color_Manager.
You will find more details by downloading:
|
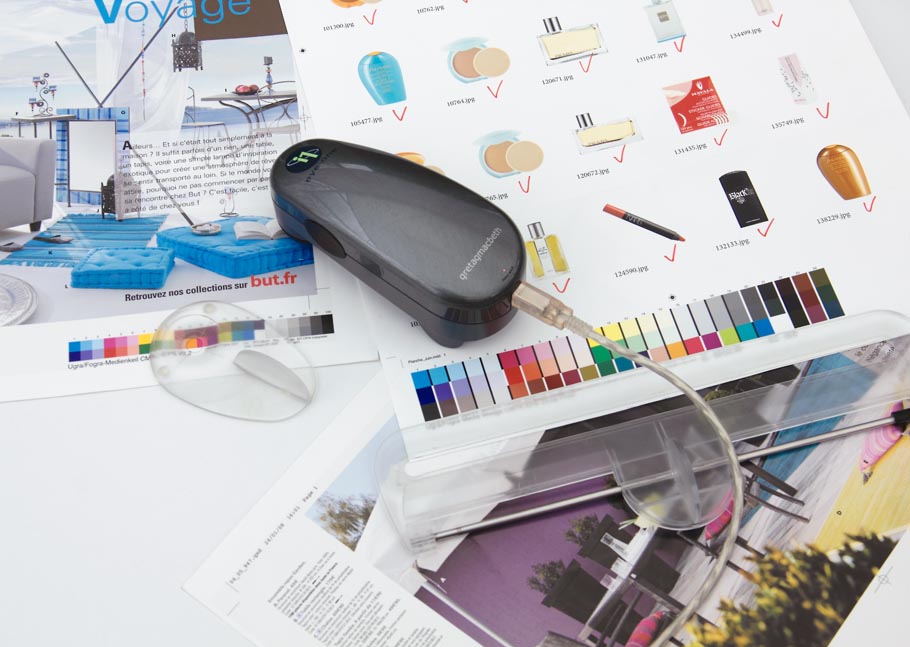
|
|